Transportation
Transportation Injection Molding
Never before have there been so many options for transportation. Whether on container ships crossing the ocean, jumbo jets traversing the skies, or trucks navigating the highways, transportation fuels world commerce. It also gets us where we need to go. We rely on buses, bikes, taxis, and even electric vehicles daily to get from point A to point B. Underpinning all these options — often out of sight and out of mind — are plastics.
Plastics are crucial across the entire spectrum of the transportation industry. From interior cosmetic finishes to components critical for functionality, plastic injection molding allows businesses in the transport sector to hit milestones and cost targets more reliably. Plastics make that possible without compromising existing commitments to quality. However, challenges often remain when working with molding manufacturers. Long lead times, inconsistent part quality, and poor communication all contribute to less-than-satisfactory project outcomes.
With Reliant Plastics, avoiding these shortfalls and embracing the full potential of integrating injection molding in transportation is seamless. Better connections in your product supply chains can transform results. From producing parts intended to resist heavily corrosive environments to developing sleek and modern cosmetic components for consumer-facing applications, our capabilities are broad, and our passion is unmatched.
Key Benefits of Using Plastics in Transit
Why are plastics the future of transportation?
Glad you asked. Working exclusively in metal is expensive and time-consuming, not to mention problematic because of weight, corrosion, and design flexibility. Plastic, on the other hand, offers a versatile solution for transportation, with injection molding itself functioning as a highly reliable manufacturing method. Let’s take a closer look at the advantages of plastic injection molding and considerations for why you should make the switch now.
1. Improved Fuel Economy
Plastic components weigh far less than their metal counterparts. Transitioning from metal to plastics can result in weight savings of anywhere from 30% to 50%. Converting parts into plastics reduces more than just the weight of each part, but also the weight of the entire vehicle. Lighter-weight vehicles require less power to move, which translates to better fuel economy. These benefits can be unlocked at any scale, from small craft to jumbo airliners, but most use cases in transportation for RIM molding today remain automotive-focused.
2. Design Flexibility
With jet injection molding for plastic parts, we can create molds for many component styles, enabling the engineering of various parts for use in transportation settings. Plastic also opens the door to more versatility in the assemblies and systems used by your projects, allowing you to use variations on one part design or create an interchangeable system that makes maintenance easier than ever.
3. Material Versatility
Transportation equipment may experience a wide range of physical conditions. For internal components, that could mean withstanding high heat or chemical exposure. With many different polymer types now available, finding a plastic with the correct physical profile is a cinch. More material options mean more pathways to transitioning components into plastic.
4. Improved Performance at Lower Cost
Plastics can exhibit superior durability and longevity with the right material selection. Trust in corrosion resistance, heat resistance, and other physical attributes without going over budget. Transportation injection molding projects can be highly cost-effective, yielding better prices per part than metal.
Accessing These Benefits
These advantages can give your business a competitive edge or pathway to improving production outcomes. New molding projects can represent an important investment in the future successes of your transport undertakings. With Reliant on your team developing, testing, producing, and enacting quality-control over the components and products you require, reaping benefits is inevitable.
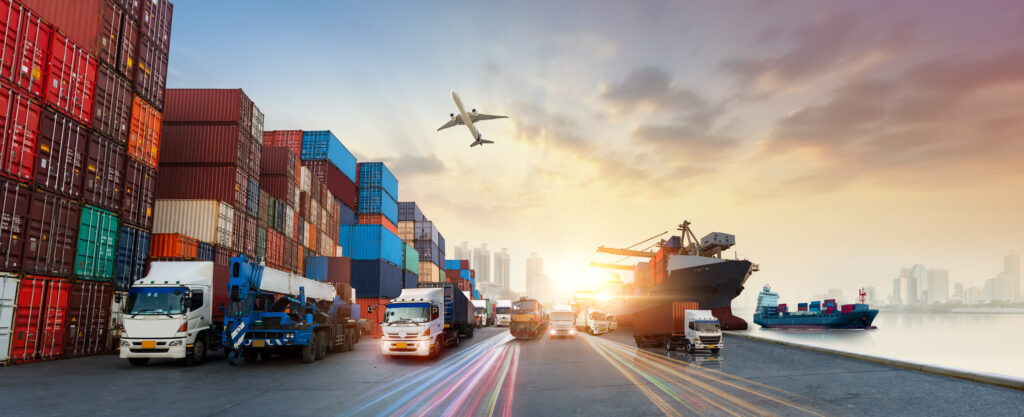
Create a Supply Chain Without Weak Links
Managing injection molding logistics can be a challenge in the transportation sector. Each vehicle’s supply chain can be pretty long and involve many suppliers. Harmonizing these elements is essential for success.
Challenges Facing Modern Supply Chains
Common issues and concerns that might give some manufacturers pause when considering investing in an injection molding project include:
- Long turnaround times.
- Shipment delays.
- Irregular quality control.
- Poor process visibility and insight.
The right partner for packaging and transportation mold manufacturing and product support makes all the difference in quelling these matters. That’s where Reliant comes in.
Strengthening Supply Chains With Reliant
Over the years, we’ve seen others come and go because of the supply chain’s shortcomings. As we’ve grown, we’ve remained focused on what matters most: client satisfaction. Knowing that approval stems from efficiency, we provide our transport industry partners with large and small components, setting realistic targets and staying in constant communication about batch and order statuses. By keeping our clients informed, we hold ourselves accountable and deliver on time and on target.
Keep the World Moving With Reliant Plastics
From the clear benefits of adopting thermoplastics for use in transport applications to the ability to tap into reliable manufacturing capabilities, the next step should be clear. You need a domestic partner who can solve problems, improve performance, and produce more consistent long-term outcomes. You need Reliant Plastics.
Contact Reliant today to start the engines on your next project.