ADVANCED COMPOSITES
ADVANCED COMPOSITES
Advanced composite materials are game-changers for manufacturers across a huge range of industries. Composites deliver new and exciting alternatives to traditional materials for the fabrication of everything from high-grade aerospace components meant to survive in space to down-hole drilling parts facing the extreme heat conditions of subterranean oil and gas exploration.
For industrial operators, there is significant value in exploring these materials and investigating ways to streamline or improve the components you already rely on in your products. However, adopting advanced composites often represents a unique challenge for businesses. These special materials demand the right equipment, knowledge, and both proven and novel manufacturing processes to produce reliable results.
At Reliant Worldwide Plastics, our experience and understanding regarding injection molding have led us to develop a broad base of ability for working with advanced composite plastics. Where other manufacturers may limit their material selection, we embrace a wide variety of specialized and challenging options to better serve our clients across industries.
Others may work with only a few materials, but Reliant never shies away from working with cutting-edge composites and resins. With the manufacturing know-how critical for avoiding high scrap rates caused by improper manufacturing, we offer our partners a clear pathway to valuable benefits, including weight reductions, strength improvements, and superior finished products.
Why Manufacturers Choose New Composites Plastics
Up to 50% lighter
Same strength
High-temperature capability
Outstanding flame, smoke, and toxicity resistances
Reduced manufacturing costs
Integrate complex shapes and geometries
Available in any color and texture
Repeatable processing
UP TO 50%
LIGHTER
SAME STRENGTH
HIGH-TEMPERATURE
CAPABILITY
OUTSTANDING FLAME,
SMOKE, TOXICITY
REDUCED
MANUFACTURING COST
INTEGRATE COMPLEX
SHAPES & GEOMETRIES
AVAILABLE IN ANY
COLOR AND TEXTURE
REPEATABLE
PROCESSING
Reliant’s Extensive Materials Expertise
There’s never been a better time to investigate working with a composite materials manufacturer. Lowering the price per finished part, reducing part weight and creating savings for consumers in areas such as fuel economy are all possible with the right experience and the correct materials.
Each composite material has unique strengths and drawbacks. Choosing the best material for your applications is not always easy. With Reliant Worldwide Plastics, our partners can explore creating solutions that are injection molded from more than half a dozen different cutting-edge materials. What are these materials?
PEEK:
Short for “polyether[BM1] etherketone,” PEEK thermoplastics offer high-performance characteristics across many applications. Highly resistant to moisture, an excellent insulator, and chemically resistant, PEEK is a valuable resource for applications in the oil and gas, aerospace, automotive, and marine industries and other high-tech scenarios. Due to its high heat tolerance (in excess of 300° Celsius) and[BM2] chemical resistance[BM3] and inherent lubricity, it is an ideal resin for lighter-weight components that would typically be made of metal.
PPS:
Polyphenylene Sulfide, a semi-crystalline thermoplastic with outstanding chemical and temperature resistance. Inherent flame retardancy and excellent electrical characteristics makes PPS idea for electronic connectors and housing applications. PPS boasts the broadest resistance to aggressive and corrosive chemical available in a plastic. Inert to steam, strong bases, fuels and acids to 200°C. PPS is also available in a FDA-approved grade and is USDA
ULTEM®/PEI: ULTEM®
Polyetherimide resins are incredibly strong and durable in high-temperature applications. Its ability to withstand repetitive high-temperature cycles make it an ideal polymer for defense and aerospace, where flame resistance and low smoke and tox emission is critical, as well as medical sector applications, in which autoclave sterilization is common. ULTEM®/PEI does not fail under these conditions even after repeated exposure to high temperatures which could cause failure in other thermoplastic components.
FST:
Short for “flame, smoke, and toxicity,” thermoplastic resins that qualify for the FST label feature a chemical makeup that confers critical safety benefits. In interior passenger-facing applications in transportation, such as in airplanes or subway cars, resins that form seats and other components must be able to withstand fire without allowing their organic polymers to release excessive amounts of toxic smoke.
IXEF 1521:
A 50% glass-reinforced polyarylamide resin, IXEF 1521 is a strong, very stiff material that also exhibits high flow properties that are ideal for the formation of very thin wall components. Known for the glossy, highly cosmetic finished parts that IXEF produces – unlike most other glass filled materials that typically have a rougher low cosmetic finish, IXEF 1521 is a tricky material that not all injection molders can handle. RWP understands how to best leverage this material’s properties for any project.
Complēt™
A family of carbon and glass polymers by PlastiComp, this material exhibits a very high strength-to-weight ratio. The Complēt™ composite range is one of the best solutions for metal replacement and lightweighting projects. Long fiber products such as these can reduce a component’s weight by nearly half compared to a comparable all-metal assembly.
Other Carbon- and Glass-Filled Polymers:
We’re adept at working with all these materials and many other types of carbon-filled or glass-filled resin. Fiber reinforced resins are on the cutting edge of the industry today, and we understand how to approach fabrication to produce long-lasting and cost-effective components and tooling.
Our versatility and experience in this area make Reliant Worldwide Plastics the ideal partner for redesigning and lightweighting your existing components.
RELIANT-LITE Advanced Overmolding for Custom Composites
Despite their cutting-edge nature, composites are not the ideal solution for every application. Using epoxy as a binding agent often means that some composites are only as strong as the glue they use. In high-stress, high-use environments, repetitive strain may cause the delamination and eventual failure of thermoset composite materials. Such a failure point negates many of their initial material advantages and demands a better solution.
To address these concerns, Reliant has created and patented our unique Homogeneous Connective Technology (HCT), now available as RELIANT-LITE®.
HCT bypasses the typical concerns surrounding delamination by overmolding thermoplastic carbon fiber substructures with a unique process using a chemically-compatible material. During the manufacturing process, this material forms an intrinsically strong chemical bond with the substrate material, forging the two pieces into one.
This process allows for additional load-bearing capabilities while extending part longevity, and the overmolding process also enables the creation of an aesthetically pleasing exterior. Color and texture are both within our control using the HCT process.
Ask us today about how RELIANT-LITE® can deliver exceptional results for metal-to-plastic conversion projects in the advanced composites industry.
Which Industries Benefit the Most from Our Capabilities?
Whether you pursue solutions with our patented RELIANT-LITE® processes or investigate how to rely on the advanced composites we’ve listed above, many industries can take full advantage of these materials.
Aerospace
There are few places where weight matters as much as it does in the aerospace sector. Every pound you can remove from the dry weight of an airplane translates directly into fuel economy savings. Components produced with advanced composites and RELIANT-LITE® overmolding can replace food tray tables, seat arms and video shrouds, brackets, flooring materials, and much more for broad weight savings.
Energy
Composite materials suppliers continue to provide critical support in the world of renewable energy, with wind turbines showcasing the large-scale benefits of advanced materials manufacturing. The stiffness of these special compounds and their long-term resistance to wear make them well-suited to work in this industry, and their roles in the oil and gas sector.
Oil & Gas
From downhole and subsea oil resources to support power plants to lightweight materials installed onboard off-shore oil rigs, we can produce a broad range of advanced composite parts ideal for use in corrosive, high-temperature environments.
Mass Transportation
Just as in the aerospace industry, mass transit systems must seek ways to reduce costs and emissions while maintaining the ability to deliver valuable service to passengers. Advanced composites are ideal for replacing armrests, seat assembly components, window components, and many other parts on mass transit vehicles.
Electric Vehicles
EVs are the future of road-based transportation, and advanced composites play a starring role in pushing forward their capabilities. From power system components that exhibit a high degree of dielectric resistance to consumer-facing components in the cabin that must exhibit appealing aesthetics, we’re ready to plan and produce the parts that you need for EV manufacturing.
Adventure Sports
Advanced composites aren’t just useful for creating lightweight tools for the adventurous, such as stronger snowboards, skis, skateboards, and other pieces of equipment—they’re also ideal for making them attractive to the eye. Overmolding softer thermoplastics on top of lightweight core materials can result in products that both perform well and please consumer tastes.
Maritime/Marine
Components made for a marine environment need to withstand challenging conditions and routine exposure to some of the world’s harshest elements. Advanced composites are ideal for use in decking and bulkheads while providing flexible options for interior components.
Industrial
Streamline production equipment can reduce wear-and-tear by replacing common industrial machinery components with metal-to-plastic conversions in a composite resin. Advanced composites are an excellent choice in areas from light manufacturing to heavy-duty assemblies in highly basic or acidic environments in which resistance to corrosion is a must-have.
Building & Construction
The opportunities for advanced composite usage in construction are unlimited. Applications include creating reinforcing materials for masonry construction, column work, and even shielding a structure from the elements.
Telecommunications
Tiny components within handsets are one potential application, but advanced composites also have a role to play in telecommunication infrastructure. Thanks to their electrical resistance and ability to act as an insulator in many conditions, there are a host of high-level applications for these materials in telecommunications.
Hunting/Fishing/Guns
The elite hunter always looks for an edge. That edge can come in the form of a hunting bow with pulley components that can last for tens of thousands of pulls or a firearm with a lightweight design made possible by the replacement of common metal components with stronger advanced composite materials.
Explore Advanced Injection Molding Opportunities Today
Reliant Worldwide Plastics features a large and diverse team of experienced engineers and skilled individuals ready to deliver high-value injection molding solutions for these industries and many others. Our global capabilities enable us to produce parts at low or high volumes as needed.
Tap into our insight for help with your next project. Contact us for help.
RELIANT-LITE®
Homogeneous Connective Technology, or HCT, allows RWP to injection mold carbon-fiber infused substructures that can be overmolded with a customer, facing, aesthetically pleasing, thermoplastic shell in any texture or color desired. The patented HCT manufacturing process chemically bonds the structure and overmold at a molecular level, intrinsically resulting in a two piece component that acts and performs as one while eliminating common composite defects such as delamination and separation.
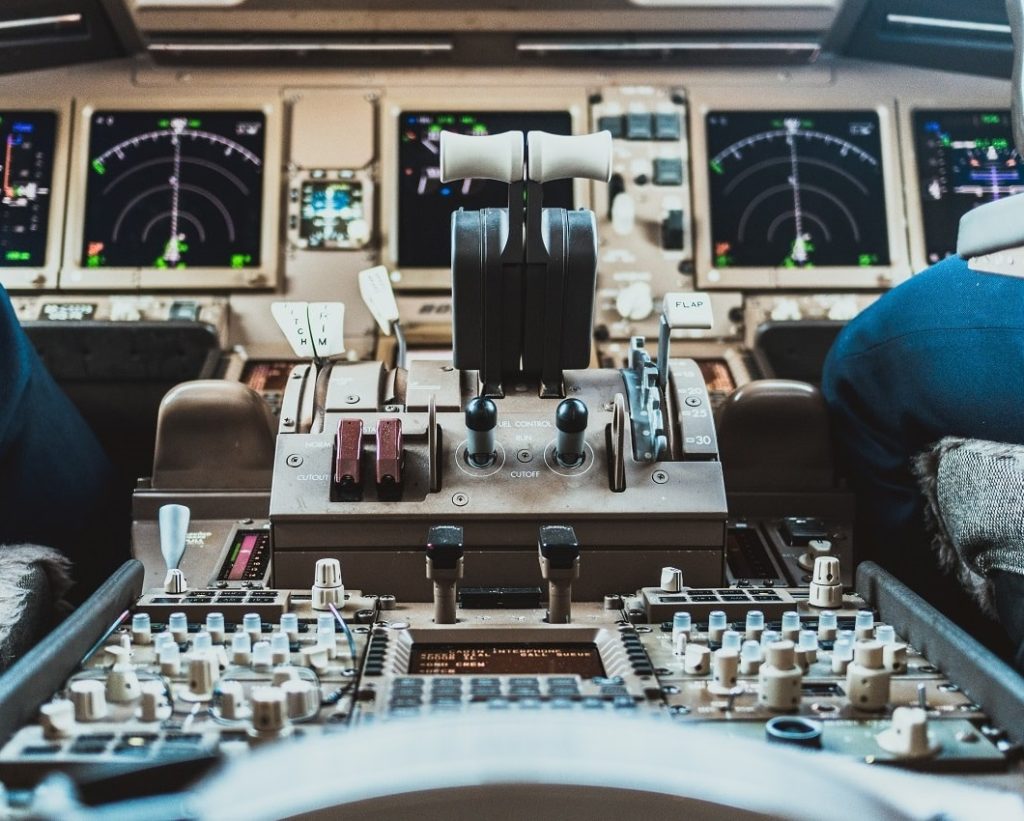
RELIANT-LITE®
RELIANT-LITE® is able to have mounting fixtures molded into the part as opposed to traditional composites or thermosets that must rely on fasteners and adhesives. This allows for mounting fixtures to have homogeneous connectivity with the part further enhancing the load it is able to withstand.
RELIANT-LITE® Applications:
- Tray Table Assemblies
- Armrest Assemblies
- Video Shrouds
- Foot Rests
- Armrest/Legrest Spreaders
- Brackets
- Substructures
- Boxes
- Almost any interior component currently being made from metal
UNLIKE COMPOSITE PARTS:
- There is no epoxy that can cause sharp edges in impact
- Parts can be thermoformed to many different shapes
- Thermoplastics is a relatively rapid process
- Thermoplastics are far more Green than composites
- There are no brittle resins in use joining unlike materials (non-homogeneous)
- No polyesters
- The strength of our product is NOT based on glue
UNLIKE CARBON OR GLASS FILLED PARTS:
- The placement of the continuous fiber strands is exact each time, glass or other filled materials is not sustainable for testing since placement of the fibers can take an infinite number of variations – failure at key strength points is inevitable.
- Reliant’s HCT parts flex similar to metal parts and don’t break with jagged edges like carbon filled resins have been prone to do in testing.