Most plastic parts are small and look quite simple in their finished form. In truth, a lot goes into designing and manufacturing these parts to ensure they are just right. In most cases, plastic injection molding is the process used for the fabrication of such components. It’s a process with its fair share of potential pitfalls and defects, all of which can delay projects, ruin entire production batches and set manufacturers back thousands of dollars.
There’s an upside, though: experts have had decades of molding to use for understanding the causes of these problems and what to do. In this article, we’ll look at some of the most common injection molding defects and the solutions that can help avoid the
Flow Lines
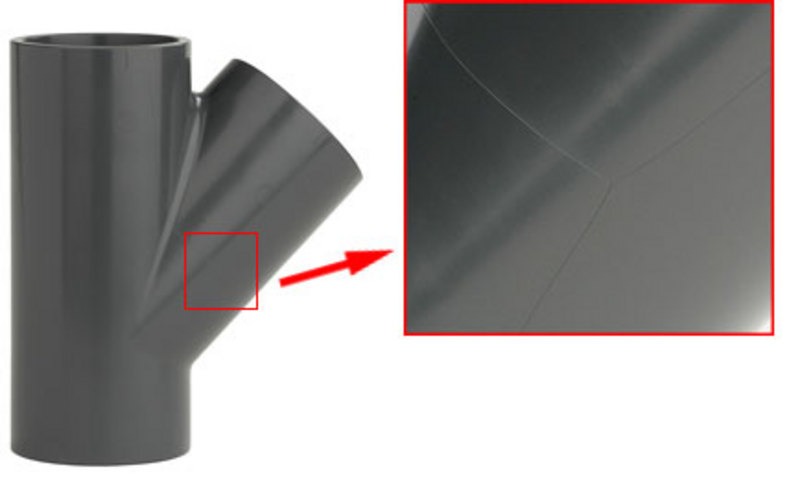
Problem
Flow lines from injection molding are streaks, lines or random wavy patterns that show on plastic molded components. They usually appear as a slightly different color than the rest of the part. Flow lines occur because of the cooling that takes place in the mold. Sometimes, different parts of the material in a mold cool at different rates. The material that cools earliest often leaves behind flow marks.
Solution
Several solutions can address flow marks in injection molding. Increasing the speed of injection when filling a mold is the simplest option. Plastic starts cooling the moment it enters the mold, so if there is a slow fill rate, some of the material will already begin cooling before the entire mold cavity fills. Another option is to focus on the wall thickness of the mold, which can avoid consistency issues with cooling.
Warping
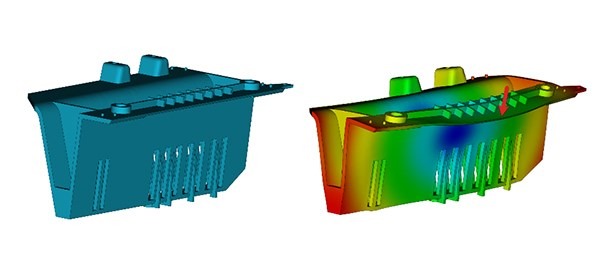
Problem
During the cooling process, the plastic in a mold shrinks and contracts slightly. Sometimes, this process occurs unevenly, which can cause the part to warp from the stress of internal forces. A warped plastic component will be bent or twisted in ways that could potentially render it unusable. Uneven cooling can even introduce additional plastic defects, such as cracks and fractures, which could compromise the part’s integrity under stress.
Solution
Inconsistent cooling often occurs in molds where the cooling process occurs too rapidly. Rapid cooling increases the risk of uneven shrinkage, putting undue strain on different design parts and causing warping.
Controlling the speed and consistency of the cooling process is vital to avoid this problem. You can do so by designing your plastic molds to have more consistent wall thickness or by altering the temperature of the plastic material or the mold itself. You may also consider using a different plastic compound if your original material is particularly prone to shrinkage
Burn Marks
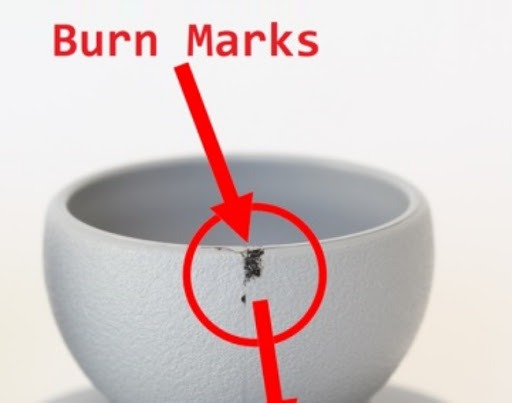
Problem
Burn marks on plastic-molded parts manifest as sections of black or discolored material on your plastic part. In most cases, the burns only affect the surface of the plastic, which means they look worse than they are. You’ll see much discoloration on the part’s surface, but the plastic beneath the burn mark will be fine.
In some rare cases, the plastic may burn badly enough to compromise the integrity of the plastic, in which case you’ll have to discard the part.
Solution
This molding defect appears when trapped air in the mold or the plastic resin itself becomes overheated. The two most common causes are 1) excessive heating of the plastic resin before injection and 2) injection speeds that are too fast, which can trap hot air in the mold.
The solutions, therefore, are to reduce both the resin temperature and injection speed. Other options include ventilation in the mold itself (to give trapped air a way to escape) and shortened cycle times for the molding process.
Sink Marks
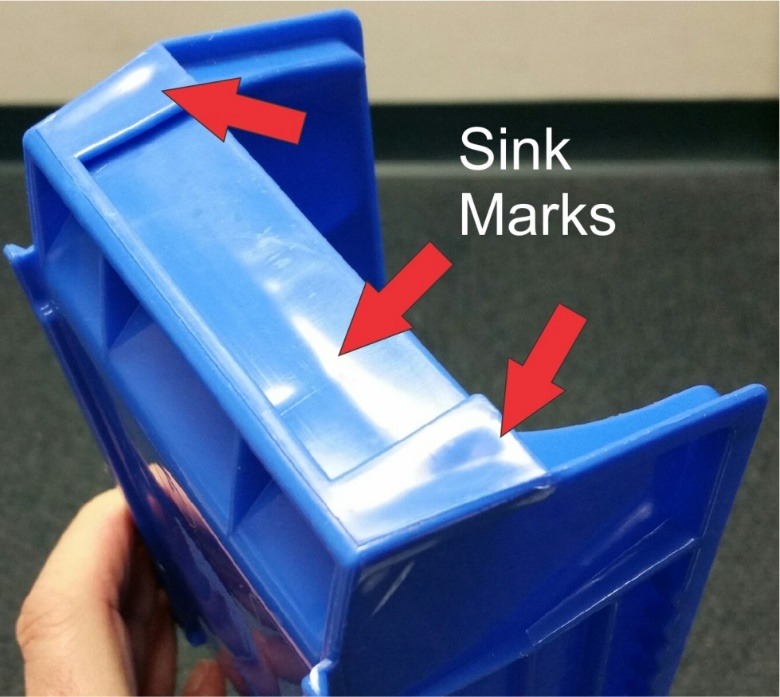
Problem
Sink marks are injection molding defects that resemble small dents or craters on the part’s surface. They are the result of uneven mold walls. Specifically, thick wall sections that don’t allow the part to sufficiently cool in areas of larger mass will cause sinking.
When this happens, the thickest sections of the part can’t cool as quickly as the thinner walls; thus, these thicker sections continue to shrink, causing material from the surface to sink into itself. This process leaves behind small but noticeable depressions in the part’s surface.
Solution
Usually, the cause of this plastic defect is simple: the exterior parts of the molded component cool too slowly. Thus, if shrinkage occurs in the part’s interior, the material will naturally pull from the surface to fill that space. The surface layer of plastic has not yet cooled enough to be fully stable.
Solutions include reducing the wall thickness of the mold to allow for faster surface cooling or increasing the holding pressure in the mold to compensate for shrinkage
Voids
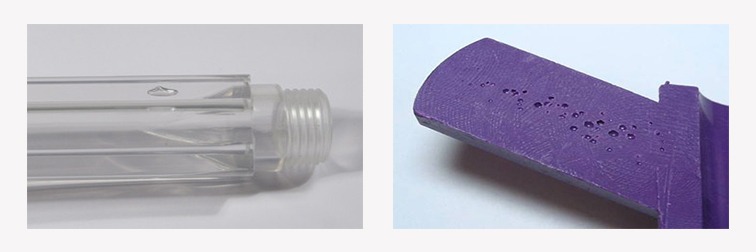
Problem
In the world of molding defects, vacuum voids are the opposite of sink marks. Where a vacuum causes sink marks in the middle of the part, pulling material down from the surface, vacuum voids are air pockets or bubbles that appear on the surface of a molded part.
In most cases, these bubbles occur due to insufficient holding pressure. High enough holding pressure levels will essentially force all air out of the mold, leaving no opportunity for air pockets to form. Lower holding pressure allows air to stay in that environment, sometimes resulting in vacuum voids. These defects are usually on the minor end of the spectrum but can affect a part’s strength and structural integrity.
Solution
Increasing the pressure at which you inject material into your mold can help force out air pockets and avoid vacuum voids. Lower-viscosity plastic resins are also worth trying out if you have been struggling with vacuum voids, as they are less likely to cause the air bubbles that create an injection molding defect in the first place.
Setting Up for Successful, Quality Production
These types of plastic injection molding defects are not the only ones that a plastic manufacturer may face, nor are the proposed injection molding solutions the only options you will have to solve each problem. Ultimately, you will likely need to do some trial and error to find the right balance between the materials you use, the temperatures of the resin and the mold, the thickness of the mold walls, the speed of injection, and other factors. There are many variables with plastic injection molding, and as you can see, those variables can sometimes lead to defects in your finished parts.
Contact Reliant Plastics
At Reliant Worldwide Plastics, we offer a diverse team with an incredible depth of experience gathered over decades providing many industries with a top-shelf injection molding solution. Using a combination of rapid prototyping and advanced computer-aided design, including mold flow analysis, we engineer solutions for our partners that avoid common defects, reduce wastage, and improve outcomes from one end of the process to the other. Discover solutions for an array of scenarios, from unexpected material difficulties to using injection molding for small parts without a problem.
Contact us today to learn more about how we can help and request a quote for your project.